
PRODUCTS
We have been producing rotary regenerative heat exchangers for more than 30 years. During this time, we have gradually developed into a globally known manufacturer of heat recovery exchangers.
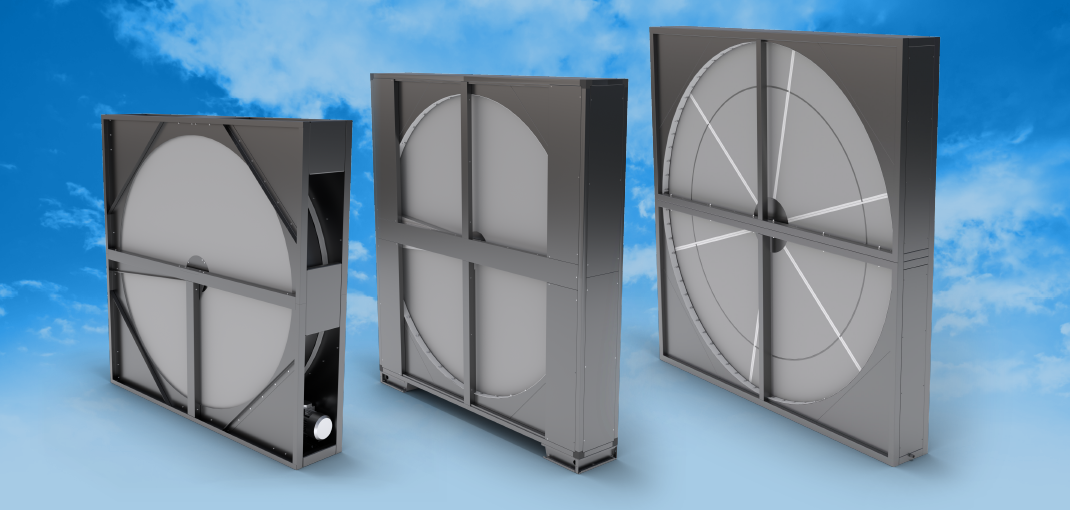
Kastt’s highly efficient rotary heat exchangers are an energy-saving solution for all ventilation and air-conditioning systems, from small apartments, through office spaces, production halls to special industrial applications and the largest industrial buildings.
Kastt rotary heat exchangers stand out for their cutting-edge technology, production precision and, above all, their unique heat and moisture transfer efficiency. Thanks to innovation and continuous development, we always try to be one step ahead.
KASTT ROTARY HEAT EXCHANGERS
KASTT’s highly efficient rotary exchangers belong to the top of the heat recovery market. They are designed to ensure energy savings for all ventilation and air-conditioning systems, from small apartments to office spaces, hospitals, schools, production halls, to special industrial operations.
KASTT rotary heat exchangers stand out for their cutting-edge technology, production precision and high energy saving efficiency. Thanks to innovation and continuous development, we always try to be one step ahead. At the same time, we are able to adapt to customer requirements and needs.
The main advantages of regenerative heat exchangers
- High thermal energy transfer efficiency (heat and cold)
- The ability to simultaneously transfer heat energy and moisture
- Low susceptibility to rotor icing
- Small installation width in air-handling units
The design of KASTT rotary exchangers is optimized as much as possible to achieve maximum efficiency of heat and moisture recovery – up to 90%, thereby significantly reducing environmental impact.
The largest possible diameter of the exchanger rotor, up to 5 m, represents approx. 150,000 m3/h of nominal air volume.
The principle of rotary regenerative exchangers
Rotary regenerative heat exchangers work on the principle of energy accumulation – alternating transfer of energy contained in the exhaust air to the storage mass and subsequent transfer of this energy to the supply air. The exchanger is being regenerated.
Regeneration versus recuperation
Recuperation: Rotary regenerative heat exchangers are often mistakenly called recuperators. . In recuperative heat exchangers (cross plate heat exchangers in most cases), both air streams are separated by a solid wall. They work on the principle of heat transfer by conduction in the thin wall of the exchanger (through its heat exchange surface).
Regeneration: The great advantage of rotary regenerative heat exchangers is that, in addition to the transfer of heat energy, they can also transfer moisture, and in addition to sensible heat, they also transfer bound heat. In this way, they achieve the highest efficiency from heat recovery systems.
More information on terminology can be found in the Glossary.
PRODUCT RANGES


ASSEMBLED VERSION

WELDED VERSION
OTHER OPTIONS

H-ECO

NEW H-WAVE ROTOR

SMART SYSTEM

LABYRINTH SEALING

ZEOLITE

CLEANING DEVICE

DRIVE, CONTROL AND REGULATION
DESIGN SOFTWARE
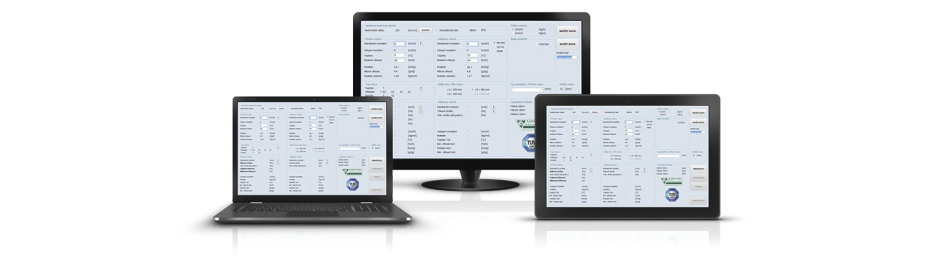